Understanding Central Lubrication Fittings: Essential Components for Efficient Machinery
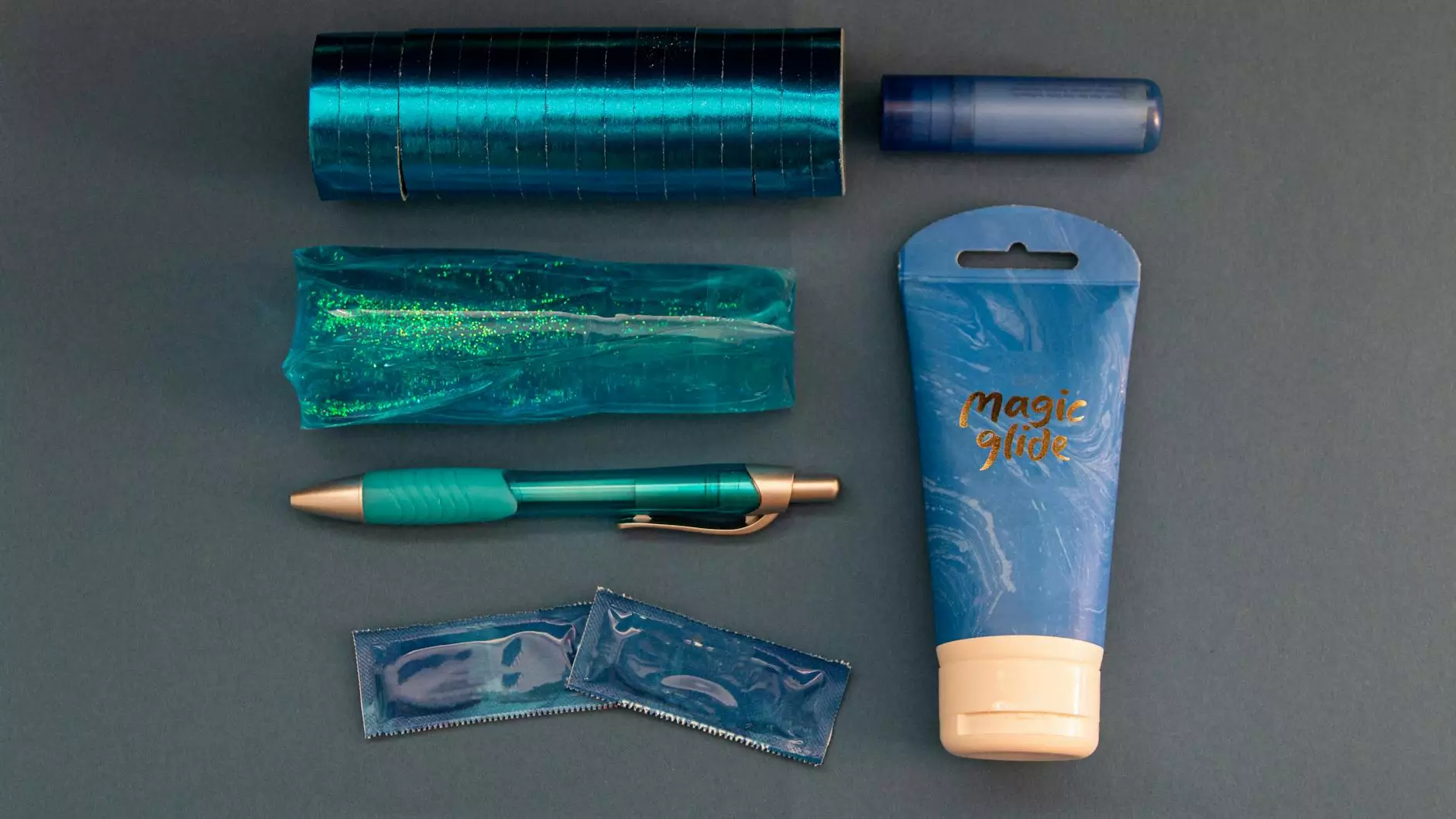
In the world of machinery and engineering, the efficient operation of equipment is paramount. One of the critical systems that contribute to this is the central lubrication system. This article will delve into the significance of central lubrication fittings, their types, applications, and how they contribute to the longevity and effectiveness of machines.
What are Central Lubrication Fittings?
Central lubrication fittings serve as the access points for lubricants within various types of machinery. These fittings are designed to deliver lubrication efficiently to the machine parts that require it, ensuring that wear and tear are minimized through effective lubrication. This system centralizes the application of grease or oil, streamlining maintenance processes and enhancing equipment reliability.
The Importance of Central Lubrication Fittings
Implementing central lubrication fittings in machinery offers numerous benefits, which include:
- Reduced Wear and Tear: Proper lubrication significantly extends the lifespan of machinery components.
- Minimized Downtime: With a central system, the need for manual lubrication is reduced, allowing for quicker maintenance.
- Increased Productivity: Consistent lubrication leads to smoother operations, enhancing productivity.
- Enhanced Safety: Proper lubrication reduces the risk of overheating, which can lead to catastrophic failures.
Types of Central Lubrication Fittings
Central lubrication fittings can be categorized based on their design, application, and lubrication approach. Understanding these types can help in selecting the appropriate fitting for specific needs. Below are some common types:
1. Grease Fittings
Grease fittings are designed to accept grease through a standard grease gun. They are common in heavy machinery where heavy-duty lubrication is required. These fittings are built to withstand harsh conditions and ensure a tight seal to prevent leaks.
2. Oil Fittings
Oil fittings are utilized primarily in systems that employ liquid lubricants. They usually feature a valve system that regulates the flow of oil into various parts of the machinery. These fittings are crucial in industries where high-speed operation of machines is common.
3. Pneumatic Fittings
Pneumatic fittings are used in systems where air is utilized for lubrication. These fittings provide a high level of control over the lubrication process, allowing for precise application in sensitive machinery.
4. Quick Couplers
Quick couplers are designed for fast and easy lubrication connections. They allow for rapid coupling and uncoupling, which can be particularly beneficial in mobile machinery where time is of the essence.
Applications of Central Lubrication Fittings
Central lubrication fittings are integral in various industries, including:
- Aerospace: Ensuring the safety and reliability of aircraft components.
- Automotive: Improving the lifespan of engine components and reducing maintenance costs.
- Construction: Maintaining heavy machinery like excavators and bulldozers.
- Manufacturing: Lubricating assembly lines and production equipment to boost efficiency.
Factors to Consider When Selecting Central Lubrication Fittings
Choosing the right central lubrication fittings can significantly impact the effectiveness of your lubrication system. Consider the following factors:
1. Compatibility
Ensure that the fittings you select are compatible with the lubricants being used and the specific equipment installed. Consider the viscosity and temperature tolerance of the lubricant.
2. Material Selection
The materials from which fittings are made should withstand the operational environment. Corrosive environments may require stainless steel or other resistant materials.
3. Pressure Rating
The fittings must meet the pressure requirements of the lubrication system to ensure effective and safe operations.
4. Fitting Size
Ensure the size of the fittings matches the machinery’s specifications to avoid issues with leakage or inadequate lubrication.
Maintenance of Central Lubrication Fittings
Proper maintenance of central lubrication fittings is critical for prolonged equipment life. Here are some best practices:
- Regular Inspection: Check fittings regularly for wear, leaks, and blockages.
- Cleanliness: Keep fittings clean and free from contaminants to maintain the integrity of the lubrication system.
- Accurate Lubrication: Utilize the correct type and amount of lubricant as specified by the manufacturer.
- Documentation: Maintain a log of lubrication activities for better tracking and improved maintenance scheduling.
Conclusion: Investing in Quality Central Lubrication Fittings
In conclusion, central lubrication fittings are essential components that play a vital role in maintaining the efficiency and longevity of machinery across various industries. Investing in high-quality fittings can yield significant returns in productivity, safety, and cost savings through reduced maintenance needs. Businesses looking for reliable and efficient lubrication solutions should consider selecting fittings from trusted suppliers like fitsch.cn, which offers a comprehensive range of products designed for various applications.
As industries continue to evolve, the demand for effective and innovative lubrication systems will grow. Understanding the importance of central lubrication fittings will empower organizations to make informed decisions that lead to better equipment management and operational excellence.