Unlocking the Future of Metal Fabrication: The Vital Role of Prototype Molded Parts
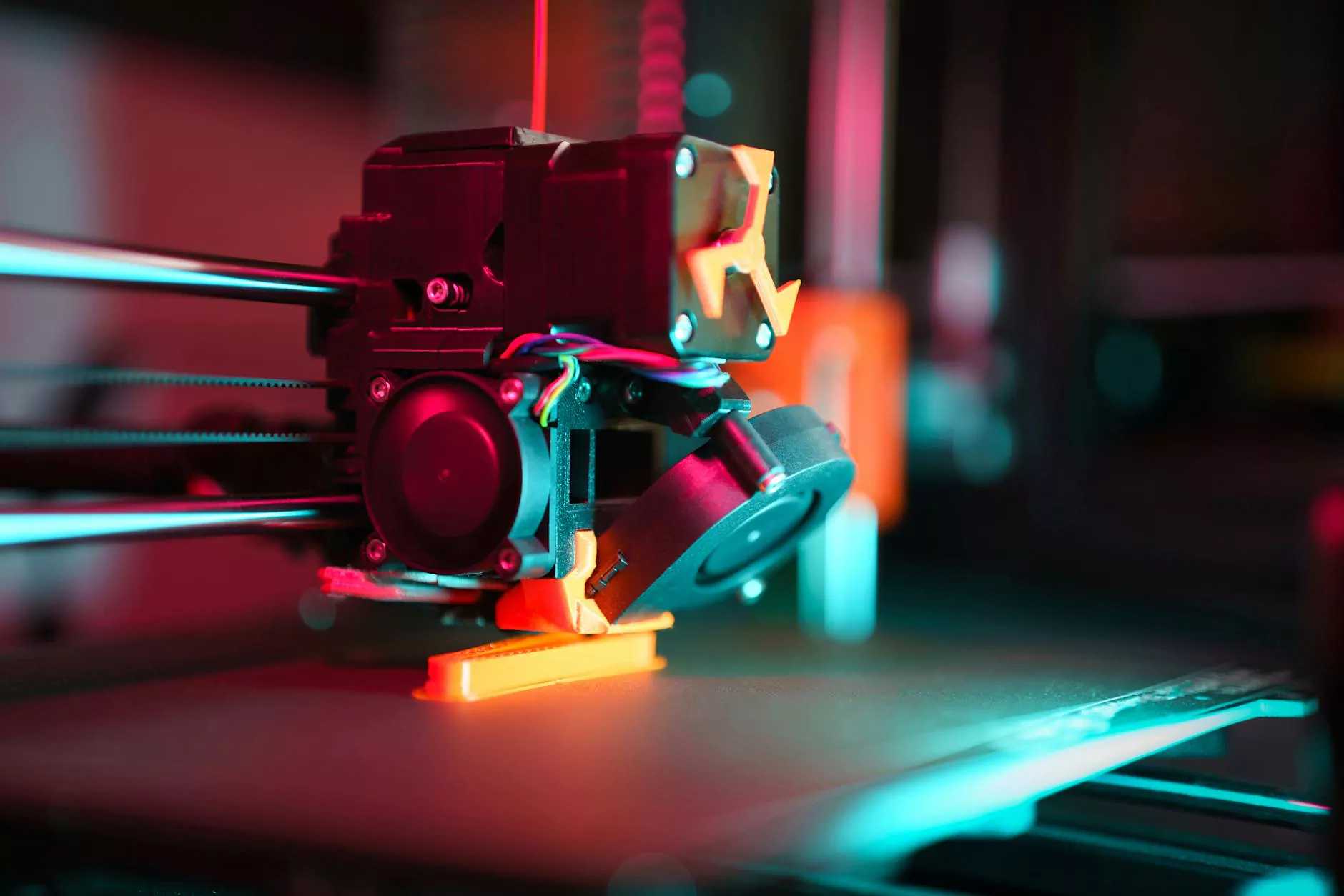
Introduction to Prototype Molded Parts
The world of metal fabrication is ever-evolving, with businesses seeking innovative and efficient methods to meet design requirements. One aspect that stands out in this journey is the production of prototype molded parts. These components serve as crucial links between concept and reality, allowing enterprises to test and refine their designs before full-scale production. In this article, we delve deep into the realm of prototype molding, exploring its significance, applications, and the transformative impact it has on businesses across various sectors.
What are Prototype Molded Parts?
Prototype molded parts are preliminary versions of products, typically created to demonstrate form, fit, and function. They are produced using molding techniques that allow designers and engineers to evaluate designs comprehensively. Made from various materials such as plastics, metals, and composites, these prototypes enable businesses to assess designs before committing to costly production processes.
Benefits of Using Prototype Molded Parts
Utilizing prototype molded parts offers numerous advantages for businesses venturing into metal fabrication. Here are some key benefits:
- Cost Efficiency: By identifying potential design flaws early, businesses can avoid the high costs associated with mass production errors.
- Time Savings: Rapid prototyping techniques shorten the development cycle, allowing quicker transition from concept to production.
- Enhanced Communication: Prototypes serve as effective communication tools among team members and stakeholders, providing a tangible representation of ideas.
- Improved Product Quality: By thoroughly testing and refining prototypes, businesses can ensure higher quality final products that meet customer expectations.
- Flexibility: Changes can be made easily during the prototyping phase, accommodating last-minute adjustments to designs.
The Process of Creating Prototype Molded Parts
The creation of prototype molded parts involves several steps, each critical to ensuring that the final product meets the desired specifications. Here’s a breakdown of the typical process:
- Design Conceptualization: Initially, the idea is fleshed out using CAD (Computer-Aided Design) software to create detailed 3D models.
- Material Selection: Depending on the application, suitable materials are chosen for the prototypes, focusing on durability, strength, and cost.
- Molding Method Selection: Various molding techniques, including injection molding, blow molding, and compression molding, are considered based on the complexity of the design.
- Production of the Molds: Molds are fabricated based on the selected designs, which can be done using CNC machining or 3D printing technologies.
- Prototype Fabrication: The actual prototype is produced using the chosen material and molding method, resulting in the first physical representation of the design.
- Testing and Evaluation: The prototypes undergo rigorous testing to evaluate functionality, aesthetics, and any potential issues that could arise in production.
- Refinement: Based on feedback from testing, necessary changes are made to optimize the design before moving forward with full-scale production.
Applications of Prototype Molded Parts
Prototype molded parts find application across various industries, showcasing their versatility and importance in product development. Here are some notable applications:
1. Automotive Industry
In the automotive sector, prototype molded parts are key to developing new models and components. They allow manufacturers to test engine components, interior fittings, and body panels without the need for extensive tooling.
2. Consumer Electronics
Consumer electronics companies utilize prototype molded parts to produce housings for devices. Rapid prototyping helps them innovate quickly and respond to market trends efficiently.
3. Medical Devices
The medical industry relies on precise prototypes for devices like surgical tools and diagnostic equipment. The functionality and ergonomics of these products can be perfected through prototype testing.
4. Aerospace Engineering
Aerospace companies require highly specialized components where safety is critical. Prototype molded parts play a vital role in ensuring that all elements are rigorously tested before final assembly.
The Future of Prototype Molded Parts in Metal Fabrication
As technology advances, the importance of prototype molded parts in metal fabrication continues to grow. Emerging trends include:
- 3D Printing Advances: Additive manufacturing technology is innovating the field, allowing for faster production and more intricate designs.
- Material Innovations: New materials with enhanced properties are being developed, broadening the scope of what is possible in prototype creation.
- Integration of AI and Automation: Automation within the prototyping process is increasing efficiency, enabling quicker iterations and better quality control.
Choosing the Right Partner for Prototype Molded Parts
Selecting a competent partner for your prototype molded parts is crucial. Consider the following factors:
- Experience: Look for a company with a proven track record in producing high-quality prototypes.
- Technology: Ensure they employ the latest technologies in prototyping and molding.
- Customization: The ability to offer tailored solutions to meet unique business needs is essential.
- Quality Assurance: Partner with organizations that prioritize quality, employing rigorous testing protocols.
- Communication: Strong communication lines are vital to ensure the project aligns with your vision.
Conclusion
In an age where innovation is the driving force behind successful businesses, prototype molded parts serve as a cornerstone in the journey from concept to market-ready products. By facilitating thorough testing, improving product design, and reducing overall costs, prototype molded parts are indispensable in the realm of metal fabrication. Companies that embrace these technologies position themselves for success in an increasingly competitive landscape.
For businesses like Deep Mould, understanding and utilizing the potential of prototype molded parts can unlock new avenues for product development and success. With careful planning, a focus on quality, and an eye on the future, the integration of prototype molded parts will undoubtedly shape the next generation of innovative solutions in the metal fabrication industry.