The Evolution and Significance of Precision Die Casting in China
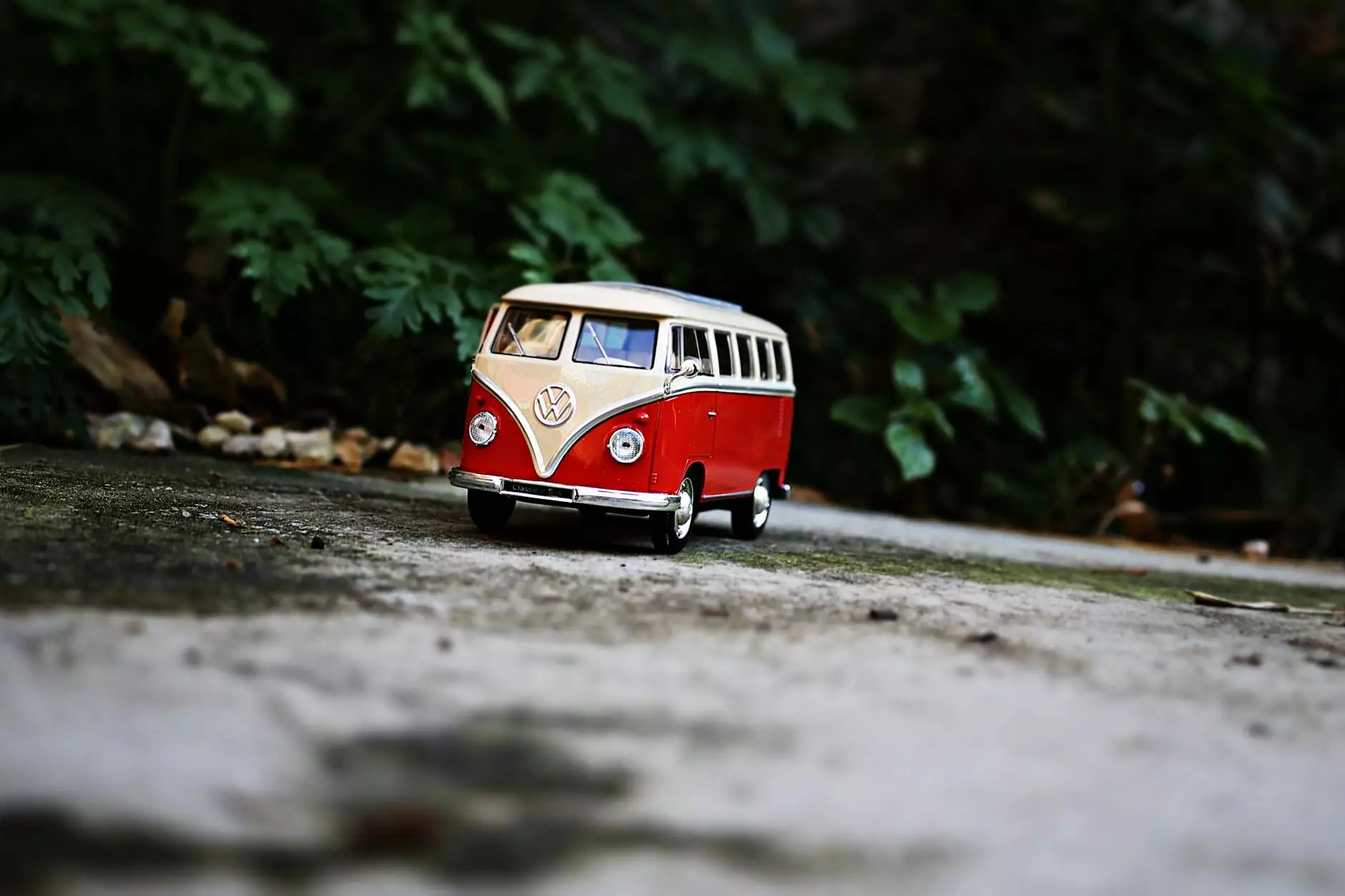
In recent years, precision die casting in China has become a cornerstone of the manufacturing industry, driving innovations and fostering economic growth. This advanced process delivers high-quality metal components with intricate geometries, making it the go-to choice for a variety of industries including automotive, aerospace, electronics, and consumer products. As industries continue to emphasize efficiency and quality, the need for precise, durable components remains paramount.
What is Precision Die Casting?
Precision die casting is a metal casting process that utilizes high-pressure to force molten metal into reusable molds, known as dies. This technique allows manufacturers to produce complex shapes with exceptional accuracy and surface finish. The applications of this method have expanded tremendously, showcasing its versatility across different sectors.
Key Benefits of Precision Die Casting
- High Precision: Parts produced through die casting possess tight tolerances, ensuring they fit perfectly in their intended applications.
- Excellent Surface Finish: The quality of the surface can reduce or eliminate the need for secondary finishing operations.
- Complex Geometries: Die casting accommodates intricate designs that would be challenging or impossible with other methods.
- Economic Efficiency: High production rates coupled with minimal waste make this process cost-effective for large scale production.
- Diverse Material Options: Various metals (including aluminum, zinc, and magnesium) can be used, adapting to the specific requirements of different applications.
The Role of China in the Global Manufacturing Landscape
China has emerged as a global manufacturing powerhouse, particularly in the field of precision die casting. The country's robust infrastructure, skilled labor force, and competitive pricing have made it a prime destination for businesses seeking high-quality metal components. Deep Mould is one of the leading manufacturers in this field, leveraging state-of-the-art technology and design expertise to deliver exceptional products.
Technological Advancements in Die Casting
With the ongoing advancements in technology, the die casting process has significantly evolved. Incorporating automation and computer-aided design (CAD) into the manufacturing process allows for greater precision and efficiency. Modern die casting facilities in China utilize:
- Robotic automation: To enhance precision and reduce human error.
- Advanced CAD software: To design complex mold structures that maximize production efficiency.
- 3D printing: For rapid prototyping and testing of designs before full-scale production.
Applications of Precision Die Casting
The wide-ranging applications of precision die casting in China highlight the method's versatility. Here are some of the key industries benefiting from this process:
1. Automotive Industry
The automotive sector significantly relies on die casting for the manufacture of engine blocks, transmission cases, and structural components. The lightweight nature and strength of components produced through die casting contribute to improved fuel efficiency and overall vehicle performance.
2. Aerospace Sector
In the aerospace industry, the need for lightweight yet durable components is critical. The precision and reliability offered by die cast parts make them ideal for applications such as aircraft fittings and structural members, where performance and safety are paramount.
3. Electronics and Electrical Equipment
Electronics manufacturers prefer die casting for producing housings and heat sinks that protect sensitive components while ensuring effective heat dissipation. The precision of these castings plays a vital role in the functionality and longevity of electronic devices.
4. Consumer Products
From household appliances to tools, many consumer products utilize die-cast components. The ability to produce complex shapes in high volumes at a lower cost appeals to manufacturers aiming to meet consumer demands efficiently.
Deep Mould: A Leader in Precision Die Casting
Deep Mould stands at the forefront of the precision die casting industry in China. With a commitment to quality, innovation, and customer satisfaction, Deep Mould has established itself as a trusted partner for a wide array of sectors. Here are the reasons why Deep Mould excels in this competitive landscape:
1. Expertise in Design and Engineering
The team at Deep Mould comprises seasoned engineers and designers who understand the nuances of die casting. Their expertise ensures that every component is designed for optimal manufacturability and performance. By utilizing advanced simulation tools, they can anticipate potential manufacturing challenges and address them proactively.
2. State-of-the-Art Manufacturing Facilities
With cutting-edge machinery and automated processes, Deep Mould enhances production capabilities while maintaining high standards of quality. Their facilities are equipped with the latest die casting machines, providing the ability to produce complex designs at high volumes efficiently.
3. Rigorous Quality Control
Quality is non-negotiable at Deep Mould. Each product undergoes rigorous testing and inspection to ensure it meets the highest standards. Their quality assurance team employs statistical process control (SPC) techniques to closely monitor production, thus minimizing defects and ensuring reliability.
4. Customized Solutions
Understanding that different industries have unique requirements, Deep Mould offers customized die casting solutions tailored to specific needs. Whether it’s selecting the appropriate material, adjusting tolerances, or developing specialized molds, they are committed to meeting and exceeding customer expectations.
Future Trends in Precision Die Casting
The landscape of precision die casting is continuously evolving, influenced by technological advancements and market demands. Here are some trends that are shaping the future of the industry:
1. Sustainable Manufacturing Practices
As global awareness of environmental issues grows, there is a strong push toward sustainability in manufacturing. The die casting industry is responding with eco-friendly practices such as reducing waste, recycling materials, and improving energy efficiency in production processes.
2. Integration with Industry 4.0
The rise of Industry 4.0 is transforming manufacturing by integrating smart technologies. In die casting, this means utilizing IoT devices, big data analytics, and advanced robotics to optimize production processes, reduce downtime, and enhance overall efficiency.
3. Advances in Material Science
Innovations in materials are expanding the possibilities for die casting. New alloys and composite materials are being developed, offering improved strength, weight savings, and corrosion resistance. This trend allows for even more innovative designs and applications across various industries.
Conclusion: The Future is Bright for Precision Die Casting in China
The future of precision die casting in China is promising, fueled by technological advancements, a commitment to quality, and a dedication to meeting the evolving needs of global industries. Companies like Deep Mould exemplify this progress, providing state-of-the-art solutions that not only meet but exceed industry standards. As we move forward, the integration of sustainable practices, smart technologies, and innovative materials will further solidify China's position as a leader in die casting.
In summary, precision die casting is more than just a manufacturing technique; it is a powerful driver of modern industry, embodying the principles of innovation, efficiency, and quality. With China's unmatched capabilities and expertise, the potential for future growth in this sector is unparalleled, making it an essential component of the global manufacturing landscape.
precision die casting china